Cost-effective machine guidance with robust GPS positioning
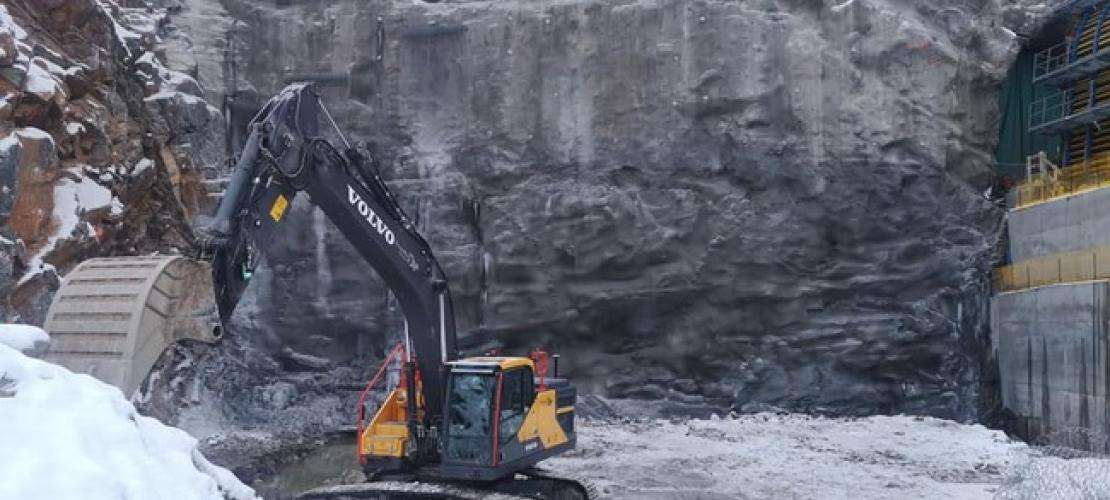
GPS/GNSS receivers for machine control and heavy machinery
“I can’t believe it!” exclaimed the operator from inside his excavator cabin, and started frantically tapping buttons on the screen, hoping to get rid of the error message that blocked his digging plan: “GPS position unavailable”. “Now the whole guidance system is down!” he opened the door of his warm and tidy cab, put on his winter boots, and stepped out into the chilly Norwegian winter air. “Now my GPS is down too,” he shook his head and joined a group of frustrated workers assembled by the new railway tracks. “My excavator’s got the latest guidance model, you guys also got some big names, and they’re are all down while Makin’s guidance is still going? I bet those guys are working way off target!”. Total stations were set up to check the angles of the slopes dug out by the excavators still working on the site, excavators with Makin’s GNSS based guidance system, a company that just a year ago started to win over the Norwegian machine control market. “It’s spot on. So how in the world do they do it?” whispered the surveyor behind the total station.
Saving costs by using highly available GNSS
GNSS receivers are not all made equal and that makes or breaks the machine’s guidance systems when projects get tough. When GNSS outages occur, guidance system integrators can easily loose around $1000/day for each idle machine. On top of that valuable time is lost and workers in the field get demotivated. Having a high quality GNSS (Global Navigation Satellite System) receiver with the right technology inside allows machine control systems to work even in the toughest environments.
Machines on the construction site described above, were used to erect metal fences protecting Follo Line (Follobanen) railroad tracks connecting two major urban areas of Oslo and Ski. The tracks run through the mountains, and high metal fences shield passenger trains from falling rocks. All the machines on the site were equipped with the latest machine guidance technology from various providers, using RTK positioning with centimeter-level accuracy. Such high accuracy is needed when digging out slopes, for example for drainage pipes. A slightly wrong slope angle, can disable the whole water drainage system.
What counts for GNSS-based machine control?
So what kind of magic allowed Makin’s GNSS-based guidance system to keep working while others went down?
Multi-constellation technology
As high metal fences went up, they created a kind of canyon around the construction site, blocking visibility to satellites needed by the GNSS guidance systems. As traditional GPS systems failed, those receivers that had access to the highest amount of positioning satellites were the "last man standing" on the construction site. Today GNSS constellations include not only the American GPS but also the European Galileo, Russian GLONASS as well as the Chinese BeiDou, which has the largest number of satellites in orbit since its latest phase 3 launch. Receivers that fully support these constellations “see” about 2 times more satellites than dual-constellation receivers. That is why receivers with access to the highest amount of satellites have the best positioning availability when the sky is partially obstructed by high structures or machinery.
Multi-frequency
The more signals a receiver can access the more information it can gather from available satellites. For example for the Galileo constellation multi-frequency receivers make use of 5 signals, while dual-frequency receivers can make use of only 2 signals. This makes positioning of multi-frequency receivers more reliable in areas where the number of visible satellites is limited. Multi-frequency receivers also improve positioning accuracy by resolving ionospheric errors which happen as GNSS signals pass through the atmosphere.
Multipath mitigation
Metal fences around the construction site not only block low-elevation satellites but also generate reflected GNSS signals causing “multipath”. Advanced tracking technology such as APME+ reduces the errors caused by the reflected signals to minimize the impact on the positioning calculation. This allows the receivers to work better under multipath, which can occur around large smooth structures, buildings or rock faces.
Shock and vibration resilience
Excavators were digging in a rocky bed sustaining harsh vibrations and shocks. Algorithms such as LOCK+ ensure smooth tracking even during rapid changes of the antenna position.
Low latency
An excavator cab can make a full rotation in under 5 seconds. At this speed even a small delay of reported position can result in a wrong digging location. Having a high update rate with low latency ensures a stable control loop and a smooth digging plan execution.
“Robust GNSS receivers in our guidance systems helped us get the reputation we needed to become number one machine control company in Norway in under two years,“ said Ruben Hensen, Chief Operating Officer at Makin. “Septentrio application engineers were always there to answer our questions and help with system optimization.”
GNSS positioning technology for toughest environments
Accurate machine guidance speeds up construction projects by over 30% and reduces CO2 emissions by cutting down fuel consumption. Such guidance systems depend on accurate positioning, but the built-in GNSS receivers require advanced technology to be able to operate in challenging environments such as near high rock faces, under foliage or close to large structures. By using robust high-quality receivers in machine control systems, saves machine idling costs and repair costs ensuring smooth project execution and completion. Some GNSS providers work together with their clients to optimize and fine-tune their positioning solutions to their client’s specific needs. As Makin’s excavators demonstrated, GNSS with advanced technology and algorithms works in the most challenging environments. Tough GNSS, helping get the toughest jobs done.
Watch this video to find out how excavator operators benefit from robust GNSS built into the Makin guidance system.
Related:
- Brochure: GNSS Interference - how to detect and mitigate
- Brochure: GNSS spoofing - how to detect and protect your receiver
- Customer Story : Machine control systems that work in the most challenging environments